Adam SP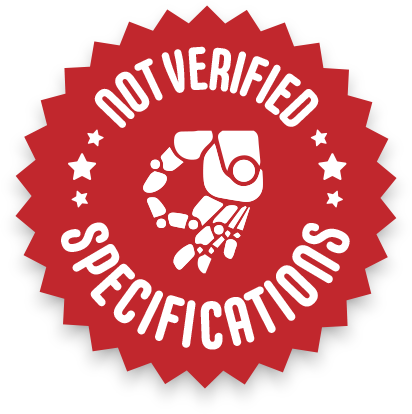
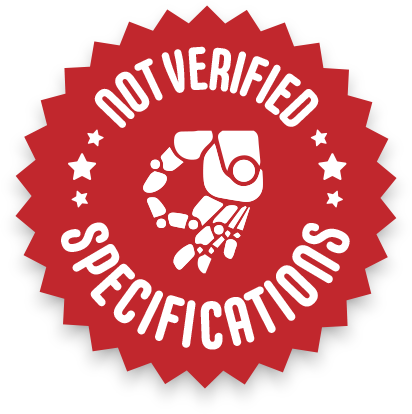
ADAM SP is PNDbotics’ 1.67 m‑tall, 62 kg humanoid robot that couples 41 degrees‑of‑freedom hardware with reinforcement‑learning control, giving industries a modular, developer‑friendly platform for safe, human‑like automation.
Humanoid.Guide skill score: 4/10 This score is calculated as the combined total of Navigation and Manipulation performance.

Specifications and details:
Availability | Prototype |
---|---|
Nationality | China |
Website | https://pndbotics.com/ |
Degrees of freedom, overall | 41 |
Degrees of freedom, hands | 7 |
Height [cm] | 167 |
Manipulation performance | Score 2 |
Navigation performance | 2 |
Max speed (km/h) | 6 |
Strength [kg] | 5 |
Weight [kg] | 62 |
Runtime pr charge (hours) | 2 |
Safe with humans | Yes |
CPU/GPU | Not specified |
Ingress protection | Not specified |
Camera resolution | Not specified |
Connectivity | Not specified |
Operating system | Not specified |
LLM integration | Not specified |
Latency glass to action | Not specified |
Motor tech | PND Smart Actuator (PSA) |
Gear tech | Integrated transmission |
Main structural material | Integrated transmission |
Number of fingers | 10 |
Main market | Industrial automation, service robotics |
H.G skill score | N/A |
Verified | Not verified |
Walking Speed [km/h] | N/A |
Shipping Size | N/A |
Color | N/A |
Manufacturer | PNDbotics |
Description
ADAM SP represents PNDbotics’ first high‑biomimetic humanoid: a full‑size biped engineered to mirror human stature and gait while remaining rugged enough for factory floors. Standing roughly 1.67 m and weighing 62 kg, the robot targets the sweet spot between stability and manoeuvrability, making it suitable for tight indoor workspaces as well as dynamic research labs.
Under its sleek composite shell, ADAM SP packs 41 joints driven by PSA quasi‑direct‑drive actuators that can deliver peaks of 360 N·m torque without bulky gearboxes. These servo modules, plus a variable‑ratio transmission in each limb, shrink weight while boosting back‑drivability and force sensing, giving the robot soft, “human‑safe” contacts and the dexterity to lift payloads of about 5 kg. A pair of five‑fingered hands extends manipulation freedom for tool use, packaging, and lab work.
Motion planning is handled by PNDbotics’ full‑stack control system that blends imitation learning with deep‑reinforcement‑learning policies trained in simulation and transferred to the real robot. Developers tap an open‑source SDK and NVIDIA‑compatible DRL environment, meaning custom behaviours—from ladder climbing to anomaly inspection—can be prototyped rapidly and reproduced across fleets.
Initially released as a prototype, ADAM SP is aimed at industrial, logistics and customer‑service pilots where repetitive, ergonomically taxing jobs still need a human form factor. Looking ahead, PNDbotics says its modular architecture will allow quick swaps of sensor heads, battery packs and even leg units, clearing a path toward medical rehabilitation, hazardous‑site inspection and human–robot research in academia. Early customer trials are scheduled through 2025–26, with scaled production to follow pending field feedback.